CONFESSION TIME >:(
While fitting bow blocks to tidy up the bow area I peered down the run of the planking, held it up to the light and ran fngers along it (as you do).
Many of the planks are no longer glued to their neighbours, and are free therefore to twist and to run away from the sanding block!
Not a disaster, but a palpable setback!
I planked with a new bottle of PVA glue from a trade counter - it is enormously concentrated, thick and seems to dry hard and brittle. I had added as much water as I could get into the bottle, but the glue was still too viscous. I normally use PVA well diluted so that the water penetrates wood fibres. So I have probably caused this failure by using the glue without diluting it enough.
I am certain that there is nothing wrong with the glue - indeed the quality is just too good for my need with porous woods.
So, how do I recover from here?
There isn't an overall problem - because I will be covering the whole hull with at least tissue and dope, which will bond the whole enchilada together.
However I would like to re-bond the planks before finishing the sanding. Hence the method has to allow me to sand afterwards.
My favourite plan at the moment is to dollop the same pva (better diluted) onto the inside of the hull, and squooge it with a squoogee into the gaps between the planks - they can move enough to allow this to happen.
If I have run strips of insulating tape down the outside to prevent the glue marking the bottom, this should work.
In fact, while there is wet PVA on the inside of the planking I could lay down strips of fleece to bond it all together
Any better advice, please?
MOTOR MOUNT
The plan method is vertical formers with semicircular cutouts for the motor - which is held in place by a metal strap tensioned by self-tappers into some blocks on the base
The base is designed to fit exactly beween two of the bulkheads, more or less level
I will be folllowing this generally, but I prefer rubber bands to hold the motor down (or tywraps) and I like to prevent the motor spinning with some form of rubber friction mount.
So its out to the garage to try the hole saw on some of the same ply as used for the formers. The nearest hole was about 3mm in diameter bigger than a 540 motor - perfect
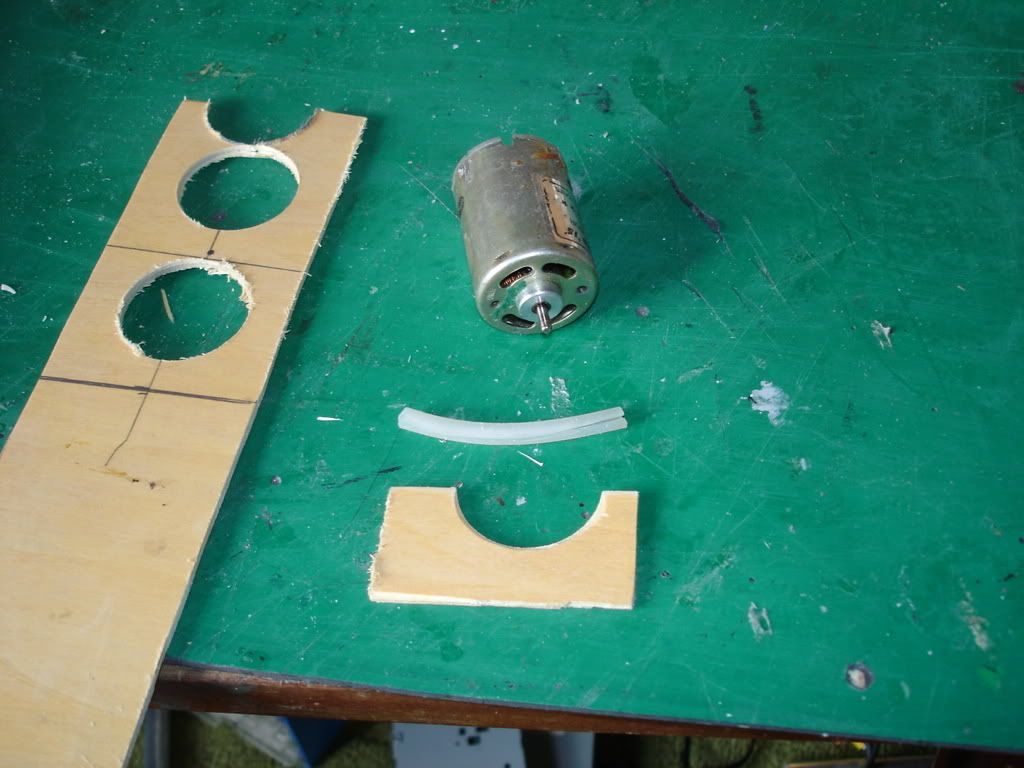
a length of silicone fuel tubing slit along one side makes a great packer-and-friction device
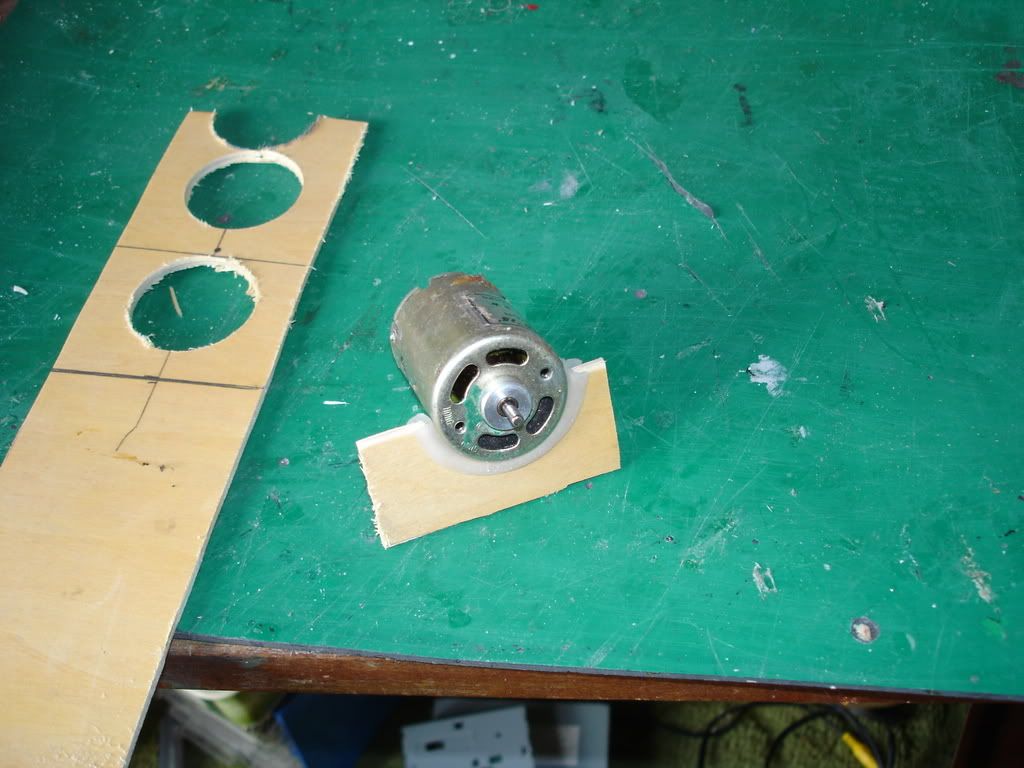
This will work well - I need to make a bit of liteply to fit between the relevant two formers, (I would sit it on a couple of 1/4 square bearers glued to the face of the bulkhead) - I could even just screw it down to the bearers so that it could be changed out for the brushless ratmotor later in life - or the twin zenoahs if AndyN proves persuasive
andrew (unnumbered but genuine)